[ad_1]
In a transfer to embrace sustainable steelmaking, British Metal has unveiled a £1.25 billion plan to switch two blast furnaces at its Scunthorpe plant with electrical arc furnaces. This follows the UK authorities’s dedication in September to speculate as much as £500 million in the direction of an electrical arc furnace at Tata Metal’s Port Talbot plant in south Wales.
This technique of steelmaking can use as much as 100% scrap metal as its uncooked materials, leading to a major discount in carbon emissions. It’s the way forward for steelmaking.
Metal is an unimaginable materials and for good cause. It’s the world’s mostly used steel as a result of it’s sturdy, sturdy and recyclable, making it the right materials for all the pieces from skyscrapers to electrical automobiles and photo voltaic panels. Greater than 1.8 billion tonnes of crude metal have been produced globally final yr. That quantity is simply anticipated to develop because the world transitions to a extra sustainable future.
The UK makes use of round 12 million tonnes of metal annually. And in 2022, it produced slightly below 6 million tonnes, contributing to round 2.4% of the nation’s greenhouse gasoline emissions.
Electrical arc furnaces
There are two primary metal manufacturing strategies. Presently, Port Talbot and Scunthorpe use the blast furnace-basic oxygen furnace technique. The aim of the blast furnace is to separate iron ore extracted from the bottom into its part elements: iron and oxygen.
A type of carbon, usually coal, combines with the oxygen within the iron ore. The outputs of this course of are iron and carbon dioxide. The fundamental oxygen furnace is then used to transform the iron into metal.
As a world common, this technique of steelmaking emits round 2.32 tonnes of CO₂ per tonne of metal produced.
An electrical arc furnace works by producing a high-temperature arc between graphite electrodes, utilizing electrical energy because the vitality supply. This arc is then used to soften steel inside a chamber.
Utilizing this technique, as much as 100% scrap metal can be utilized because the uncooked materials, whereas the blast furnace-basic oxygen furnace technique can solely use a most of 30% scrap. A swap to the electrical arc furnace technique may scale back emissions to 0.67 tonnes of CO₂ per tonne of metal produced when utilizing 100% scrap metal.
Sooner or later, it is usually attainable the electrical energy wanted for electrical arc furnace processes may come from 100% renewable sources, whereas a type of carbon will all the time be wanted to scale back iron ore when utilizing the blast furnace technique.
Recycled metal
Metal is essentially the most recycled materials on this planet, and so scrap metal is rapidly changing into an important uncooked materials. In 2021, the worldwide metal trade recycled round 680 million tonnes of scrap metal. This equates to financial savings of just about 1 billion tonnes of CO₂ emissions, in comparison with utilizing virgin metal manufacturing.
In 2021, greater than 8.2 million tonnes of metal scrap was exported from the UK. If collected and sorted extra rigorously, utilizing this materials domestically may present each environmental and financial worth, by serving to to fulfill rising nationwide demand for metal.
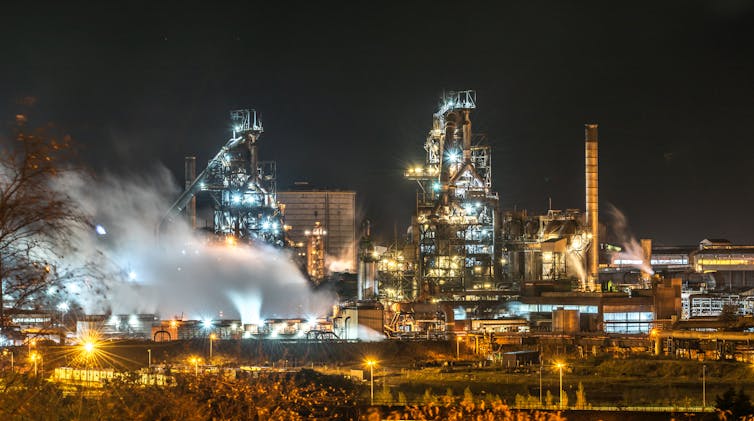
Christopher Willans/Shutterstock
We all know that metal produced with an electrical arc furnace can have totally different properties to blast furnace produced materials. A big consider that is the standard of scrap metal used within the electrical arc furnace – if the scrap metal high quality is low, then so will the standard of the output.
With that in thoughts, there’s a want for analysis, innovation and abilities growth to make sure this transition to lower-carbon steelmaking strategies is profitable.
Discovering and sorting the suitable forms of scrap materials, confirming materials properties and rising provide chain understanding of electrical arc furnace steelmaking are all needed for a variety of metal merchandise to proceed to be made within the UK.
Sustainable steelmaking
There’s a race throughout Europe to safe funding for sustainable steelmaking applied sciences. Hybrit is a fossil-free metal challenge in Sweden between a number of main metal producers and is already underway.
This follows plans to speculate nearly €40 billion (nearly £35 billion) in low-emission steelmaking applied sciences over the following 20 years. Additionally in Sweden, the corporate H2 Inexperienced Metal has secured €3.5 billion (£3 billion) to construct a hydrogen-powered metal plant.
In July 2023, the German authorities introduced €2 billion (£1.7 billion) of assist for Thyssenkrupp, the metal multinational. And that was on high of the €3 billion (£2.6 billion) it had beforehand introduced to assist the nation’s industrial inexperienced transition. A
ArcelorMittal, the second largest metal producer on this planet, has additionally introduced inexperienced funding of their vegetation in Belgium and Spain, totalling greater than €1.2 billion (£1.5 billion).
Whereas the UK authorities has no printed industrial technique, different organisations have produced roadmaps for decarbonised steelmaking within the UK.
A report by the Vitality Transitions Fee, a world coalition of vitality leaders dedicated to net-zero emissions, outlined plans for investing in low-emission steelmaking in early 2023. With the suitable stage of presidency and personal sector funding, the UK may develop into a world chief in inexperienced steelmaking – however solely it acts now.
As world temperatures proceed to rise and the local weather emergency deepens, the necessity for a decarbonised metal trade is bigger than ever. Decrease carbon strategies of metal manufacturing are the way forward for the trade each within the UK and around the globe.
[ad_2]
Source link